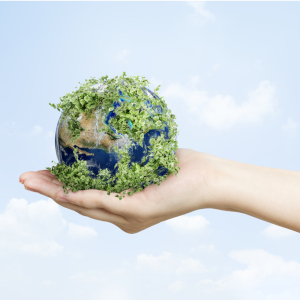
ABOUT IT
Processes and procedures to mitigate the environmental impacts intrinsic to the final disposal and treatment of its waste, as well as to capture opportunities in the fields of reduction and reuse.
The Zero Landfill project was adopted with the aim of boosting solid waste management at all of Faber-Castell Brasil's production plants, with the main focus on the company's largest industrial plant: the one located in the municipality of São Carlos/SP (the subject of this case), which is also considered to be the largest Eco-pencil factory in the world, also capturing opportunities in terms of waste reduction and reuse. The São Carlos plant accounts for an average of 90% of all the waste generated by Faber Castell Brasil.
In terms of reducing waste generation, the company has achieved a 48% reduction in waste since the start of the project, largely based on investment in machinery to recover sawdust as briquettes to sell as a by-product for energy use. With regard to the reuse of waste, the company has implemented an internal energy recovery process for its by-products which, if left untreated, would become waste: The by-products generated (wood waste) as part of the production processes in São Carlos/SP are transformed into briquettes and supply the boilers at its own plant, generating energy for its own production processes.
Another part of this waste is sent (sold) to generate energy in third-party production processes, contributing to a more circular economy and avoiding verticalization in the disposal of waste on the market.
Results and Objectives
A 48% reduction in the volume allocated. The company also made some important moves:
(a) In 2015, Faber Castell began to dispose of sawdust and pencil waste for composting instead of landfill, before disposing of it for co-processing in 2019.
(b) In 2017, segregation was improved and "miscellaneous" waste (Miscellaneous non-recyclable production process waste) was sent to composting and co-processing instead of landfills.
(c) In 2019, the sludge from the ETE was sent to effluent treatment
With regard to changes in waste disposal methods, since the start of the project it has been possible to divert 11,700 tons of waste from the landfill since 2015, an average of 1,037 tons/year.
The by-products generated (wood waste) in the São Carlos/SP production processes are transformed into briquettes and supply the boilers of its own plant, generating energy for its own production processes.
The company has implemented an internal energy recovery process for its by-products which, if left untreated, would become waste:
The company has contracted partners to package, segregate, transport, dispose of and give the final treatment to the waste generated. In addition, considering waste generated by the use of products (post-consumption stage), the company has the Post-Consumption Reverse Logistics program, in partnership with external partner Terracycle, which aims to promote environmentally appropriate disposal for writing instruments. Open to the public, anyone can create their own "writing instrument brigade", collect and send materials for recycling and proper environmental disposal.
SDGs
External Certification
International Commitments
National Commitments
More info